What Is Body Armor Made Of?
There are a ton of different sizes, weights, shapes, and protection levels of body armor. So we often get the question, “what is body armor made of?”
It’s a great question, and knowing the answer can help you choose which options are right for you. We’ve previously discussed this in another blog post discussing the concept of “expiration” of body armor, but we’re going to go a little more in-depth today. If you’ve been looking for something to get a little more in-depth about what it is you’re trusting your life to, we’re happy to help.
What Is A Bulletproof Vest Made Of?
You might know soft armor as a, “bulletproof vest.” While the industry has largely shied away from this term, it’s still popular amongst Hollywood and the general public. Soft armor ‘bulletproof’ vests are rated only for handgun munitions, and rifle munitions require a higher level of protection. Level II and IIIA soft body armor is made to be highly protective against handgun munitions such as 9mm, 45 ACP, and more. And, they’re nearly identical to the naked eye.
Simply put, Level II and IIIA are are both made by stacking layers of Para-Aramid (generally known as ‘Aramid’ or ‘Kevlar’) and/or Ultra High Molecular Weight Polyethylene (‘UHMWPE’, or ‘Dyneema’) material. Kevlar and Dyneema are well-known leading brand names in the Aramid and UHMWPE material fields, respectively. The amount of layers required varies by the particulars of the materials you’re using. There are many different aramid varieties, just as there are many UHMWPE varieties. Each has different price, strength, and other material properties.
Level II armor simply has fewer layers than Level IIIA armor and is marginally less protective against higher threat handgun rounds like .44 magnum. So-called ‘bulletproof vests’ are made of Level II and IIIA soft armor. But, it is also found in use as SAPI-shaped plate backer panels used in plate carriers. Plus, soft armor manufacturers use their same Level II and IIIA armor they use in concealable vests in accessory armor. You’ll see accessory armor in pieces like throat, shoulder, groin, and more that are often added by SWAT and military units.
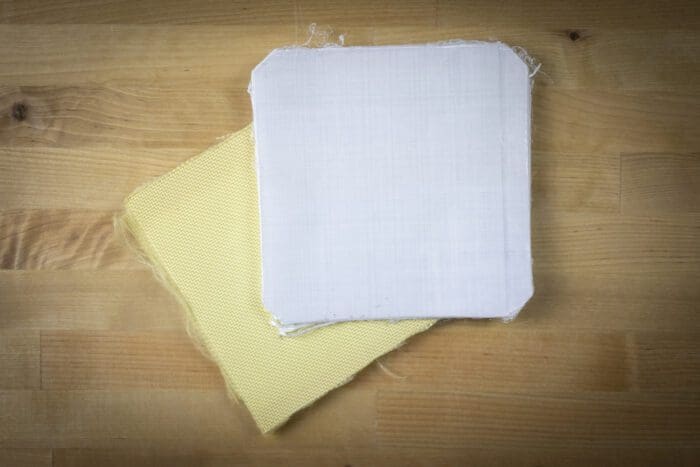
Aramid vs UHMWPE
Generally-speaking, you will find that aramid armor is softer, more flexible, heavier, and thicker than a comparable panel made of UHMWPE. RMA and other manufacturers primarily use UHMWPE in modern soft body armor today because it is so much stronger than older-generation aramid materials like Kevlar.
It’s easy to immediately tell the difference between UHMWPE and aramid materials just by looking at them. Aramids generally come in a golden or yellow color and have a woven fabric appearance. They’re flexible like fabric, too. Most UHMWPE material is a unidirectional laminate in a translucent white color. It’s more like a stiff plastic sheet than a woven textile.
Thanks to UHMWPE’s ultra-strong properties, manufacturers can use substantially less mass and volume of UHMWPE to achieve the same ballistic standards versus aramid. Aramids still remain relevant in certain respects. Aramid fiber has natural fire resistant properties that UHMWPE struggles with. Plus, aramid tends to be substantially less expensive than UHMWPE. That means you can have a high level of ballistic resistance, fire resistance, and a soft & comfortable wear experience at a low price. But if ultra thin and lightweight is your preference, UHMWPE is the only choice.
Sometimes, manufacturers combine aramid and UHMWPE into a single soft armor vest to get a combination of lighter weight and flexibility.
Is a concealable soft armor vest right for you? READ MORE
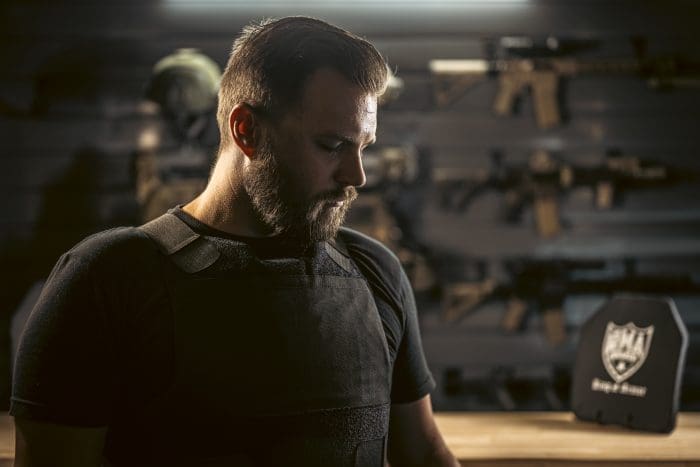
Soft Armor Wearability
The “wearability” of soft armor ultimately comes down to a subjective valuation on your part. Do you want something that’s ultra-thin & lightweight? Or, do you want something that’s softer and more flexible for all-day comfort? Both have their pros and cons, and the choice is up to you. RMA Armament offers both options in our 0214 Level IIIA Soft Armor Inserts, Protego, Contego, and Virtus Level IIIA Soft Armor Vests, and 0226 Level IIIA Hard Plates. In our 0226 Level IIIA plate, we pressed UHMWPE to make it ultra thin and lightweight. Ideally, these single-curve rigid plates are great backpack inserts. Our 0214 soft panels are great for wearing against your body thanks to their soft and flexible properties.
For other armor purposes such as hard plates, vehicles, and buildings, there are other IIIA material options. Fiberglass-reinforced polyethylene and other composites are used primarily in hard armor and as building materials. Although they are inexpensive and tough, they are inflexible and don’t make sense to use in soft armor where flexibility and thinness is paramount; especially as thinner and softer aramid and polyethylene materials continue to come down in price. We’ll touch on those a bit later.
What Is Rifle-Rated Body Armor Made Of?
Rifle-rated armor is always in a hard format. Although there are some flexible rifle-rated armor solutions on the market, they are nothing like the handgun-rated Level II or Level IIIA soft armor you may be familiar with. Fundamentally, there are a limited number of potential components in your armor plate, but each has dozens of variants. Today, we’re going to talk about ceramics, polyethylene, steel, aramid, and composites.
We often talk about how choosing which armor to purchase is a series of tradeoffs in thickness & weight, price, and protection level. At a macro level, this is generally true. But, nothing is a 1:1 swap in material science. Changing out Alumina ceramics for Boron Carbide ceramics doesn’t directly correlate.
Exchanging a tricked out Tacoma for a Ferrari gets you a faster and more expensive car. Both of these have unique roles in the automotive world that make them completely different. Whereas the Tacoma is a slow gas guzzler on pavement, it’s a highly offroad capable vehicle that takes a beating without blinking. The Ferrari, on the other hand, is the epitome of handling, speed, and acceleration on pavement. But it’s useless offroad. Armor components function in similar ways.
Ceramics
Modern rifle-rated ceramic body armor is comprised–generally, with a few outliers–of Alumina Oxide, Silicon Carbide, or Boron Carbide combined with a backer made of UHMWPE, Aramid, or composites. Mixing and matching these components gives manufacturers the ability to tailor solutions to meet specific end user needs like thinness, protection level, and price point.
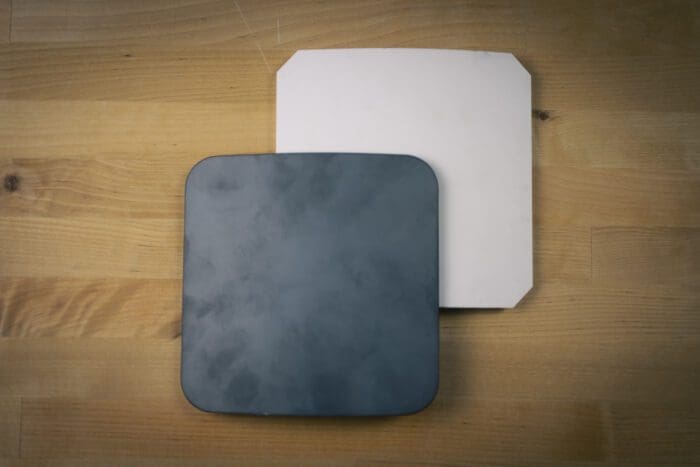
Alumina
Alumina is by far the most popular armor ceramic in the world. Affordable yet effective, Alumina makes high-grade ballistic protection accessible for everyone. Alumina’s main criticism, however, is that it tends to make plates relatively heavy. That’s true. But along with that heaviness comes a highly dense and less-brittle material. That lower level of brittleness means that the entire strike face isn’t compromised as quickly as Silicon Carbide or Boron Carbide in a multi-hit scenario. You’ll find Alumina used in our popular 1155, 1165, and 1090 series plates.
These Level IV (RF3) and Level III+ (RF2) plates combine affordability with capability. While the 1155 and 1165 are a bit heavier than our ultra lightweight Boron Carbide-based 1192 Level IV plate, they also exhibit outstanding multi-hit performance thanks to their Alumina strike face and have extremely affordable price points.
Silicon Carbide
Many experts consider Silicon Carbide to be the sweet spot for ceramics. While it’s harder and lighter than Alumina, it’s also much less brittle than Boron Carbide. Along with middle-of-the-road hardness and brittleness, it’s also a bit less expensive than Boron Carbide. However, it’s still much more expensive than Alumina comparatively. Like other armor materials, Silicon Carbide also comes in different grades.
Silicon Carbide can vary a lot in hardness, thickness, and efficacy against Steel and Tungsten projectiles. Silicon Carbide plates from different armor manufacturers are almost guaranteed to have significantly different material properties. Remember that manufacturers use a variety of materials. Ceramic manufacturers don’t make all materials equally, even if they have the same names.
Alumina from an RMA plate is American-made and distinctly different in thickness, length and width dimensions, chemical makeup, content purity, and hardness from imported strike faces used by virtually every other manufacturer. And yes, they all still say, “MADE IN USA.” Silicon and Boron are the same. Virtually no manufacturer is going to tell you where they get their materials from and specifically which materials they’re using in each product. After all, we’ve got to have some trade secrets. However, this chart demonstrates how different materials can be that all fall under one material name from just one manufacturer.
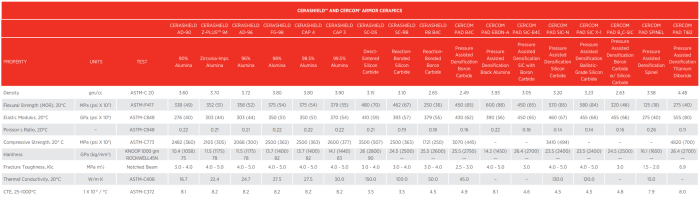
Boron Carbide
High-end users like SOCOM often choose Boron Carbide plates. Boasting extreme hardness (sometimes twice as hard as Alumina) and low density, Boron Carbide is a great solution for engineering lightweight rifle-rated armor. However like the Ferrari, it does have certain drawbacks. Boron Carbide’s high hardness means it is far more brittle. Think about hitting a brick made of clay and a brick made of glass with a hammer. The glass is much harder than the clay. But it also shatters more dramatically every time you hit it.
Boron Carbide is the same way. Alumina’s low level of crack propagation means the damaged area of the ceramic strike face remains relatively small. Boron Carbide’s brittleness means that impacts can drive cracks further through and across the ceramic. While solutions such as lamination do a decent job of mitigating that damage, multi-hit performance in lighter weight Boron Carbide ceramics is generally lesser than that of heavier Alumina ceramics.
Because of its unique chemical properties, Boron Carbide requires much higher temperatures and a more difficult manufacturing process to manipulate into a cohesive strike face. Thus, Boron Carbide ceramics tend to be much more expensive than alumina. You see the price difference between our 1155 Level IV and 1192 Level IV plates most distinctly. We price our 1155s well under $200 each. But 1192 plates reach dramatically higher prices. Both provide a high level of multi-hit Level IV protection, however the materials and engineering involved make the 1192 much more expensive to produce.
Steel
If you’re looking for steel plates, you won’t find them here. RMA offered some steel plates for a very limited time due to the volume of requests by specific customers, but it’s never been a real part of our business model. There are pros and cons to using steel as body armor, but it is our opinion (as well as that of every professional force organization) that steel is a vastly inferior material for use as armor for several reasons. Simply put, the cons wildly outweigh the pros.
First, steel plates repeatedly fail common threats from the 5.56 category. The AR-15 is the most common rifle in the United States. Additionally, you’ll find other rifles sporting the 5.56 NATO round worldwide. If you need to defeat 5.56 rounds (you do), steel is the very last choice. In fact, the NIJ recently published their 0101.07 standards which are specifically designed to prohibit steel plates from certification entirely. This is because the 0101.06 standard (and previous Level III standards) utilized the M80 NATO Steel round as a surrogate for lesser threats due to its high penetration capabilities.
Steel Continued
With normal ballistic materials such as ceramic and UHMWPE, this test makes sense. UHMWPE and ceramic plates easily defeat 5.56 threats. But because so many manufacturers sell steel as armor, many customers don’t understand that they can purchase an NIJ Certified steel plate that is called “rifle-rated body armor” that simultaneously passes M80 NATO Steel with flying colors, but that utterly fails 5.56 FMJ rounds. Given that M80 NATO Steel is essentially a non-existent ballistic threat and that steel fails the far lesser 5.56 FMJ threat it was assumed to cover, NIJ designed the RF1 protocol to prohibit the certification of steel plates. Now, steel plates will not be able to be certified at all without additional aramid, composite, or UHMWPE construction.
Steel Continued
Second, steel has a backward strength-to-weight ratio. Steel plates–while very affordable–are incredibly heavy for the mild level of protection they provide. Many are actually heavier than Level IV plates–up to 12 lbs each–and even more expensive once you add on bed liner spray to help prevent fragmentation. You’re wearing Level IV weight and only getting some Level III protection. It simply doesn’t make any sense. Don’t forget that along with that weight, you don’t have protection from the #1 most common rifle threat in the US–5.56 FMJ.
Third, steel plates have a huge problem with fragmentation. Often referred to as ‘spalling’, steel plates function in a far different way than ceramic and UHMWPE plates. While ceramic and UHMWPE plates ‘catch’ the bullet, a steel plate reflects it. Ceramic/composite and ceramic/UHMWPE plates function by using the ultra-hard strike face to break apart the bullet, slow it down, and then use the softer backing material to catch the remaining fragments. During this process, we convert the bullet’s energy from kinetic energy into heat energy.
Ceramic Isn’t The Same
A steel plate simply acts like throwing a glass ball at a brick wall. There are countless videos demonstrating this process, showing the bullet smash into the steel plate and then the fragments traveling parallel to the plate face. That means if you’re assuming a normal shooting stance, an impacting round can easily fragment directly into your face, knees, neck, arms, and thighs. All things considered, taking a round to steel armor could just as easily take you out of the fight as wearing no armor at all.
Finally, steel isn’t actually much more affordable than ceramic or UHMWPE plates. Because steel fragments bullets at the wearer, manufacturers encourage buyers to purchase fragmentation protection at an additional price. Whether it’s truck bedliner spray, double truck bedliner spray, an aramid plate pocket, or something else, the price begins to stack up quickly. Properly protect yourself from fragmentation on your steel plates, and you’ve surpassed the cost of a lighter, stronger, and frag-free 1155 Level IV plate.
UHMWPE
We use UHMWPE in a lot of armor products, but you can also get 100% UHMWPE plates. Thanks to some nerds in a lab somewhere, Ultra High Molecular Weight Polyethylene is incredibly strong and not very expensive. Once manufacturers saw how thin and light UHMWPE could make soft armor, we wondered exactly how many layers it would take to defeat rifle munitions. At some point, it will work. Thankfully, UHMWPE is so strong that it actually worked within the existing body armor hard plate template. Although they tend to be a little bit thicker than ceramic plates, UHMWPE is capable of defeating many full metal jacket rifle rounds when layered and pressed appropriately. The layer count varies depending on which specific material you’re using, but 100% UHMWPE don’t exactly tip the scales when they’re averaging about 3 pounds each.
Compared to steel or ceramics, these are unbelievably light. Level III UHMWPE plates are limited to FMJ rounds without a ceramic strike face, and provide only Level III protection (full Level III protection–including 5.56 FMJ–unlike steel). Pure UHMWPE plates are not currently capable of defeating mild or hardened steel core rounds like M855, M855A1, or M2AP. So if you’re concerned about high-speed steel, you’ll need to get ceramic. However, mild steel 7.62X39 is relatively slow, and is easily defeated by pure UHMWPE plates. Thus, these ultra light plates do in fact find their way into many modern war zones. They’re so light that they even float in water. So whether you’re operating in a marine environment or need to climb mountains, UHMWPE Level III plates can be a great asset.
“What Is Body Armor Made Of?”: Hard Armor Backing Materials
Composite
You might hear people say a particular model of armor has, “fiberglass.” They mean composites. You’ll find composite backing in almost every Level IV plate under $300. It is similar to fiberglass, in that manufacturers suspend thin strands of glass inside of a high-strength polyolefin resin. Today, that polyolefin resin is typically polyethylene. But don’t mistake ballistic composites for the fiberglass found in your home. Ballistic composite is to fiberglass what boron carbide ceramic is to a dinner plate. Composites exhibit a heavier weight, excellent ballistic resistance, and excellent resistance to deformation along with a low price. Composite material is what makes Level IV plates affordable for everyone. Virtually all manufacturers make at least several composite plates to reach lower price points.
We know composites by the names, “E-Glass,” or, “S-Glass.” Other industries use E-Glass in surf boards and buildings. S-Glass was developed from E-Glass specifically for ballistic applications, although both are suitable for body armor. S-Glass offers virtually identical weight versus E-Glass, but a slightly thinner profile. As such, S-Glass is a bit more expensive. Depending on which Level IV plates you buy under the $300-ish price point, you’re choosing composite backed alumina with E-Glass or S-Glass. There is no meaningful performance difference between the plates since we build both using an appropriate amount of material to meet the same benchmark.
Aramid
We use Aramid in both soft and hard armor, albeit slightly different variants. We make more affordable soft armor from aramid. But it’s been virtually eliminated from hard armor by most manufacturers. Simply put, it’s price and strength-to-weight ratio makes it land somewhere between composite and UHMWPE. So it’s not especially strong, not especially cheap, and lands at a higher price point than the cheapest plates. But it’s also too thick and heavy to compete with UHMWPE plates. Aramid plates in particular have also been historically far more affected by heat fluctuation and water exposure than composite or UHMWPE. All things considered, it doesn’t make much sense to use anymore. A few manufacturers still make these legacy products, but most have abandoned aramid has a viable backer material.
UHMWPE
UHMWPE is the current “gold standard” for plate backer material. Ultra High Molecular Weight Polyethylene has one of the highest strength-to-weight ratios of any material in existence. Thus, it’s perfect for armor you have to wear on your body. We use UHMWPE in our 1165 Level IV plates, 1192 Level IV (RF3) plates, 1090 Series III+ (RF2) plates, all of our Level III offerings.
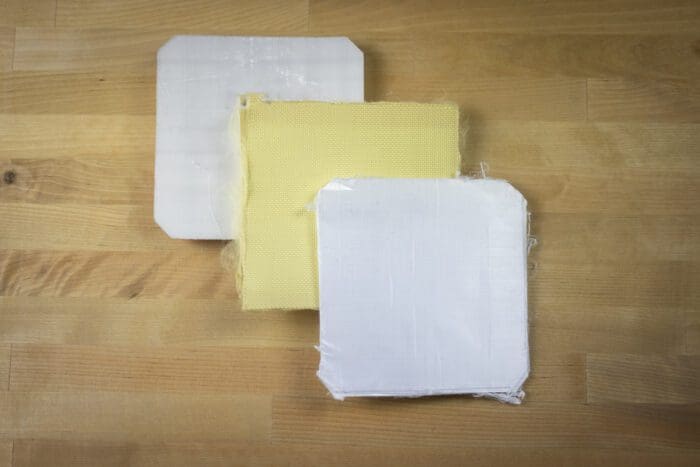
Conclusion
What is body armor made of? We do a lot of different things with different materials to make the miracle that is ballistic protection. It’s not as simple as slapping a few things together and calling it a day. Building reliable armor requires a lot of science, economics, and a fundamental understanding of the end user. We can all make armor that stops a 50 BMG or whatever outrageous cartridge you can come up with. That isn’t the hard part.
But building plates in this manner means abiding by the terms of the end-user. If we make a plate that stands up so far beyond the only testing standards in the US anyone cares about (NIJ), nobody will really understand what the product is. It will only be, “a Level IV that’s too heavy.” We already have some products that step outside those bounds in the Level IIIA+ and Level III+ category. Fortunately, the 0101.07 standard is making some headway into creating a meaningful III+ standard under the RF2 label. However, there still remains much work to be done.
The Future
Our ESRT plate is an example of a new kind of plate that stands up to the most common rifle-rated threats by providing a strong Alumina strike face with a minimal UHMWPE backer. It’s not a Level III plate, but it does perform significantly beyond a Level III plate in many important aspects. When we think about the specifics of what each material can do for us, we can start imagining how to build better armor for the real world. But it is the job of the end-user to understand what they need and what they’re buying in order to demand the right products. Today, we hope you’ve taken home some important information on what these different materials do. Together, we can save more lives.
Need a Quote for your agency? Click Here.
What Is Body Armor Made Of? FAQ
Q: Can you combine different backers like composite, aramid, and UHMWPE?
A: No. Each variant of these materials requires a different heat, pressure, and time cycle recipe when we process them in our hydraulic press. We couldn’t practically combine them if we wanted to into one stack while maintaining ballistic integrity. It might be possible to combine different pressed stacks of each into one plate, but it just doesn’t make any sense to do it. Economies of scale dictate that a manufacturer needs to seek efficiency in manufacturing.
Constantly changing materials, recipes, and adding more pieces adds expense, complicates the adhesion process, and provides no discernable benefit whatsoever for hard armor. Soft armor is a different story because it doesn’t require nearly as much machining. Raw soft armor materials paired together makes more sense in this format.
FAQ Continued
Q: What is the strongest material for body armor?
A: Titanium Diboride is an extremely strong ceramic and arguably ‘the strongest’, however it is even heavier than Alumina and comparatively expensive. On balance, it doesn’t make sense to use Titanium Diboride in armor that’s meant to be worn on the human body. Like we discussed above, Alumina, Silicon Carbide, and Boron Carbide are some of the stronger materials that make sense to use in armor, but all three have their pros and cons. You’ll have to decide if lighter weight is worth the risk of greater crack propagation and vice versa.
Q: What is the composition of military body armor?
A: US military body armor is usually a set of two things: an aramid base vest and III+ or IV type in-conjunction silicon carbide + UHMWPE hard plates. Remember that the military has their own set of standards separate from NIJ testing. Military plates may fail NIJ tests, and NIJ plates may fail military tests. SOCOM often chooses boron carbide plates that are significantly more expensive.
FAQ Continued
Q: What fabric is used for body armor?
A: Aramid is the most fabric-like material we use in body armor today. But most modern soft armor now uses UHMWPE. While UHMWPE is stiffer than aramid, it’s also much stronger. We need less UHMWPE to achieve the same level of protection versus aramid material, so UHMWPE ends up creating lighter ballistic materials.
Q: What material is bulletproof?
A: While there are a lot of materials that will defeat handgun, rifle, and shotgun munitions, there are only a few that are suitable for wearing on the human body. Those are aramids, UHMWPE, composites, alumina oxide, silicon carbide, and boron carbide.
FAQ Continued
Q: What material is 100% bulletproof?
A: Technically there is no 100% bulletproof material. Strictly-speaking, if you had enough bullets you could destroy a mountain. Real-life combat is not turn-based, so we have to manage the dynamic possibilities as best we can. The industry (among legitimate manufacturers, at least) has shied away from using the term “bulletproof” for a reason. Any armor from any manufacturer will fail at some point given enough bullets of any kind.
As you scale up the threat level in bullet hardness and velocity, that failure point approaches more rapidly. Nothing on this earth is truly bulletproof, and never will be. What we have are materials that–when constructed properly–offer a high level of ballistic resistance to a specific set of threats.
FAQ Continued
Q: Can you mix any materials you want?
A: No, materials are not 1:1 swaps. Certain backers will bond to certain ceramics better than others. It’s not that you can simply use any backer with any ceramic to build anything you want. Alumina is a great material because its chemical makeup allows armor manufacturers to adhere a huge variety of backer materials. But that isn’t always the case with silicon and boron carbide. These materials require a more specific set of material properties to adhere to a given backer. Plus, ceramics have a variety of pros and cons that must be complimentary to the backer they’re paired with.
For example, some variants of silicon carbide are largely ineffective against tungsten-based rounds. If you’re intent on using silicon carbide in a plate designed to defeat M855A1 or meet Level IV standards, you’ll need to find a backer material that compensates for the lesser SiC performance that also adheres properly. That means there is only a very narrow range of materials you can use at all. Since Alumina has more consistent munition material performance, you can more reliably pair it with a larger variety of backer materials without worrying about performance.
FAQ Continued
Q: Why don’t they make police pants out of Kevlar?
A: One single layer of Kevlar won’t defeat anything. When we talked about building soft armor earlier, we addressed the need to stack multiple layers in order to achieve ballistic resistance. But if you’re still curious what that would look like, take a gander at an EOD suit. You’ll immediately see why, “they don’t make police pants out of Kevlar.”
Q: Can Body Armor Defeat 50 BMG?
A: Humans wear body armor as a garment. There some natural constraints given the format. Sure, we can build armor that defeats 50 BMG or 20mm rounds easily. It’s only a matter of how thick and strong your ceramic and backing material is. But they become more of a liability than an asset once they hinder your physical movement, cardiovascular, and muscular endurance.
Nobody wants to wear a set of plates that are 12 lbs each. You’re armoring for a series of threats that are unlikely to ever materialize. And, you’re over-protecting for real-world threats in a way that hinders your ability to escape or fight back. When we build body armor, we want to build it to work within the constraints of what is practical to wear in a life-threatening situation. Since we know that enough bullets will break down anything, we want to orient our thinking toward how we can make the most protective item within that window.