What Is Dyneema UHMWPE?
We make a point of talking about using Dyneema UHMWPE in our armor products. We’re proud to use the top names in materials in our armor, and Dyneema is without a doubt the leading name in UHMWPE. So how does it make body armor better?
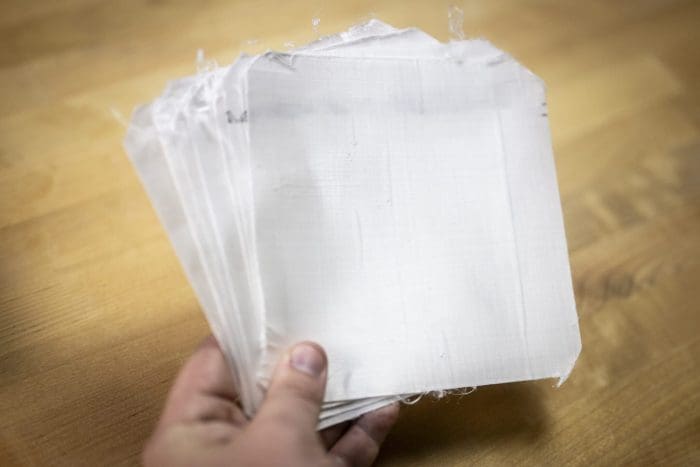
Ultra High Molecular Weight Polyethylene has been around for some time, but it has really hit its stride in the past twenty years. For decades, Kevlar®–a kind of Aramid–was the go-to solution for lightweight body armor solutions. Aramid worked well enough and remains a viable solution in many budget products thanks to its low cost. Plus, it retains significant military usage worldwide thanks to its inherent FR properties. However, UHMWPE soundly defeats Aramid in the strength-to-weight department. UHMWPE has allowed armor manufacturers to create incredibly lightweight ballistic products that are even more protective than their aramid counterparts.
The Dyneema® brand is well-known thanks to its wide-ranging applications. Outdoor recreation enthusiasts know Dyneema® from their climbing ropes and ultra-light backpacks. Dyneema is also commonly used in medical applications such as replacement joints. Additionally, it is utilized in many industrial applications such as high-strength fishing nets and sub-sea tether cables. You may have seen Dyneema used in your motorcycle jacket.
RMA uses it in many of our body armor products. Our SRT, 1090 Series, 0226 IIIA, and 1165 Level 4 all use Dyneema® to reach new levels of lightweight ballistic capability. Thanks to its incredibly high tensile strength, we’re able to replace traditional materials like E-Glass and Aramid with Dyneema®.
What is UHMWPE?
We say, “UHMWPE.” to describe a specific family of Ultra High Molecular Weight Polyethylene materials under the polyethylene tree. Polyethylene is everywhere. Different industries use it due to its high strength-to-weight ratio and extreme resistance to the forces of nature. Grocery store bags are an everyday example of the kind of strength you can expect from polyethylene products generally. UHMWPE is a specialized variant that has incredibly long molecular chains that are able to withstand extremely high forces without breaking or even significantly stretching. Avient is a large composites company that recently bought DSM, the owner of Dyneema.
Dyneema themselves have a nice presentation on how they manufacture their UHMWPE. They’re one of the only manufacturers that manufacture every bit of their product. Thus, they have the ultimate flexibility of how they want to make their UHMWPE.
From gas to UHMWPE powder
Our story starts with a gas called ethylene, which is processed in our dedicated polymerization plant to make polyethylene: a common building block used to make a wide range of everyday items, from plastic bags to shampoo bottles.
The longer the polyethylene chain, the stronger it is. In the case of Dyneema®, a chain typically contains about 100,000 individual carbon atoms (for comparison, in a plastic bag, chains of only around 10,000 atoms will do the job). Known as UHMWPE, our high-strength variant begins life as a fine UH powder.
Our backward integration drives strength forward
Other UHMWPE manufacturers buy their raw polyethylene from a supplier, which means they can’t make changes to the molecular structure of the polymer.
Dyneema® is different. Unlike others, we deploy a backward integration approach; namely, using our own raw materials to make UHMWPE powder, so we can perform molecular engineering at the polymer stage. Our engineering expertise means we can increase the strength of our fiber, ensuring Dyneema® is quite simply the strongest synthetic fiber on the market.
From powder to fiber
Next, the powder is dissolved and then heated in an extruder, using our proprietary gel-spinning process to disentangle the molecules. The heated substance is forced through a plate with hundreds of tiny holes – at which point the resulting elongated molecules begin to resemble a fiber. This is when high-strength Dyneema® begins to take shape!
But we’re not done yet. Our draw cycle process then further aligns the molecules into strands, creating an extremely strong yarn that in turn is wound onto spools, ready for use.
From fiber to unidirectional composite
Of course, before Dyneema® fiber can be used in applications such as protective body armor, it has to be transformed into a new form factor: a unidirectional (UD) material known as Dyneema® UD. In this step, the fibers are laid parallel to each other, impregnated with a water-based resin, and allowed to dry. The fully dried layer is sent to a cross-ply machine where the roll is cut into sheets. An additional layer of impregnated filaments is then placed on top and the two layers are laminated together.
The fully dried layer is sent to a cross-ply machine where the roll is cut into sheets. An additional layer of impregnated filaments is then placed on top and the two layers are laminated together. Each roll of Dyneema® UD can consist of four separate layers of unidirectional yarns, giving the material its ultra-high strength properties. Different resins can be impregnated between the layers depending on the specific properties required for the end application.
How Is Dyneema used in Body Armor?
Avient makes many variations of Dyneema for specific applications due to their unique properties. Some are better for hard armor, and others are better for soft armor. This has to do with the tensile strength, adhesive applications, bonding properties when hydraulically pressed, or how flexible or thin it is when it’s used in a soft armor vest. Armor manufacturers choose different variations depending on the properties they want their products to have.
In the case of hard body armor, it’s common to use unidirectional laminate UHMWPE. This material feels a bit like a thick plastic playing card. Avient lays individual fibers of UHMWPE next to one another and laminates them into a long sheet. We cut out this sheet into shapes we need for body armor, such as SAPI plate shapes. In order to maximize performance, we don’t cut our sheets all the same way. In each layer, we rotate the directional orientation of the material. This helps us create inconsistencies in how the bullet travels through the material. These inconsistencies mean that there is no straight or easy path for a bullet to travel. A complicated path of travel allows us to efficiently convert more kinetic energy into heat energy and reduce mass retention in the slug very quickly. And don’t forget, this material is already extremely strong.
So, we end up needing very little mass and volume of material to accomplish any given ballistic goal that we’re looking for.
A smaller footprint of material means less bulk and weight. Dyneema® UHMWPE makes our armor wearable for long periods of time.
The Benefits on Display
While we use Dyneema UHMWPE in several products, our 1165 plate demonstrates it best.
Our 1155 Level IV plate is known worldwide. 1155 has saved numerous lives in foreign conflict zones like Israel and Ukraine, as well as in the United States. It’s a sturdy, reliable plate designed with affordability in mind. However, it is relatively heavy at 8.3 lbs per plate. This weight is normal among other plates built similarly. However, we wanted to figure out a way to lighten the load without giving up the high velocity armor-piercing protection it’s known for.
First, there’s no getting around ceramic. At this point in material technology, we need ceramic to defeat high speed armor-piercing projectiles. It cannot be done with steel. We also cannot do it with UHMWPE alone. We covered this kind of thing rather extensively in another post, so feel free to check that out.
In essence, we use the existing Alumina Oxide ceramic from our 1155 series. But instead of using an E-Glass backer, we used the Dyneema UHMWPE we’ve had success with in our 1090 series.
Then, we removed the foam protective cover from the strike face. This usually accounts for almost 20% of a plate’s thickness. However, we didn’t leave it unprotected. Instead, we laminated it.
Our in-house lamination process has multiple benefits. It functions something like a flat layer of tape across the strike face. Lamination does provide some minor drop protection on its own. But the biggest benefit is crack propagation mitigation. So whether the strike face is dropped or shot, our lamination stops any localized damage from traveling throughout the plate. In many ways, it’s superior to manually protecting the face with some kind of foam. So while it protects from drop damage, it also enables better multi-hit performance.
1155 vs 1165 vs Other Level IV Plates
So when we look at these results in totality, we were able to slash 1.5 lbs from the 8.3 lb 1155. That means the 1165 weighs only 6.8 lbs. At only $249.99, there’s nothing else like it. Thanks to high-strength Dyneema UHMWPE, we were able to dramatically slash weight without giving up performance.
What’s even more impressive is that we did it without giving up any coverage. Many sub-8 lb Level IV plates achieve the ~7.2 lb mark by cutting away coverage. Others advertise their Level IV plates as 10X12 “shooter’s cut” plates. But in reality, they’re actually 9.3-9.5 inches by 11.3-11.5 inches. That doesn’t sound like a large reduction until you see it in person.
These plates often have issues properly fitting in many carriers since nobody manufacturers plate carriers to fit these odd non-standard dimensions. The truth is that what they’re selling you is an overpriced 1155 design (Alumina + E-Glass) that is 8.2-8.4 lbs in its true Medium SAPI or 10X12 form. They advertise lower weight numbers by cutting away coverage. Sure, it’s lighter weight to not wear armor. But that isn’t the point of body armor.
We saw that we could offer a superior plate in every way for the same $249.99 price as everyone else’s E-Glass plate. It’s true 10X12 edge-to-edge coverage with a Dyneema UHMWPE backer. Additionally, it’s still nearly a half pound lighter per plate than these “shooter’s cut” plates that give up a significant amount of protection.
It’s simply superior in every way. How did we make it so affordable? Don’t worry, I also wrote that one up for you as well.
Conclusion
RMA will continue to innovate using Dyneema UHMWPE in our armor products. We’re pushing the entire industry forward by using superior materials and manufacturing processes while keeping prices affordable. And yeah, we noticed that since we launched the 1165, our competitors have been forced to dramatically slash many Level IV prices. Even if you don’t buy from us, we’re still working to slim down those absurd competitive prices for you. We’re not stopping with the lightweight 1165.
We make armor by Americans, for Americans. And we do it with American materials in our factory in Centerville, Iowa.